Home » Mather + Platt » Pumps » Introduction to pumps
A Brief Introduction To Pumps
There are two basic types of pumps, fixed displacement and variable displacement. Fixed displacement pumps comprise some sort of chamber and a ram or piston mechanism that draws the fluid into the chamber, closes the inlet valves, opens the outlet valves and then discharges the fluid from the chamber. The valves can be mechanically operated by a cam arrangement or can be of the disc type that close against light springs on pressure or vacuum. Clearly, a fixed displacement pump cannot be operated against a closed valve or serious damage can occur.
Variable displacement pumps on the other hand come in a variety of types. Injector and ejector pumps use a high pressure nozzle to force a fluid through a smooth opening to create a vacuum around the nozzle. The fluid from around the nozzle is combined with the high pressure fluid and passes through the pump. Injectors are used to pump fluid into a boiler, for example, and ejectors are used to evacuate a system such as a steam locomotive brake system. Centrifugal pumps comprise some form of rotating impeller enclosed by a set of fixed vanes. Fluid enters the impeller at the centre and is forced outwards by its rotation. The speed and diameter of the impeller characterize its duty pressure, while overall size determines the flow. These types of pumps are further characterised into centrifugal and axial flow. Centrifugal pumps are generally where the direction of the incoming water is in the direction of the shaft while outlet fluid is at right angles to it. In axial flow pumps, the direction of the fluid is along the axis of the shaft at all times. A pump whose characteristics lie on the borderline of these two criteria is called a mixed flow pump. A term called 'specific speed' determines more formally the type of pump. This is the formula to calculate specific speed:
speed x (capacity)0.5 | |
specific speed = | -------------------------- |
(head per stage)0.75 | |
where speed, capacity and head per stage are all at the best efficiency point.
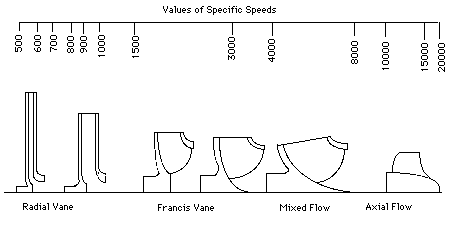
Centrifugal and axial flow pumps can be operated at closed valve without damage, though the vigorous stirring of the fluid in the pump can generate significant amounts of heat which may have adverse effects. The pump generates its highest pressure at closed valve but consumes its least energy in these circumstances. Indeed, although it would seem perverse, a pump and motor set can be overloaded by allowing too much flow through the pump.